A greener kind of battery factory
11 January, 2022
We’re driving a new standard for industrial ownership and responsibility towards the environmental impacts of manufacturing. Siting Northvolt Ett battery gigafactory in northern Sweden to harness a clean energy supply was just the beginning. Here we present insights on the engineering of circular solutions into the factory itself – an approach that’s reducing resource consumption, minimizing impacts on the surrounding environment and contributing to a commitment to build the world’s greenest battery.
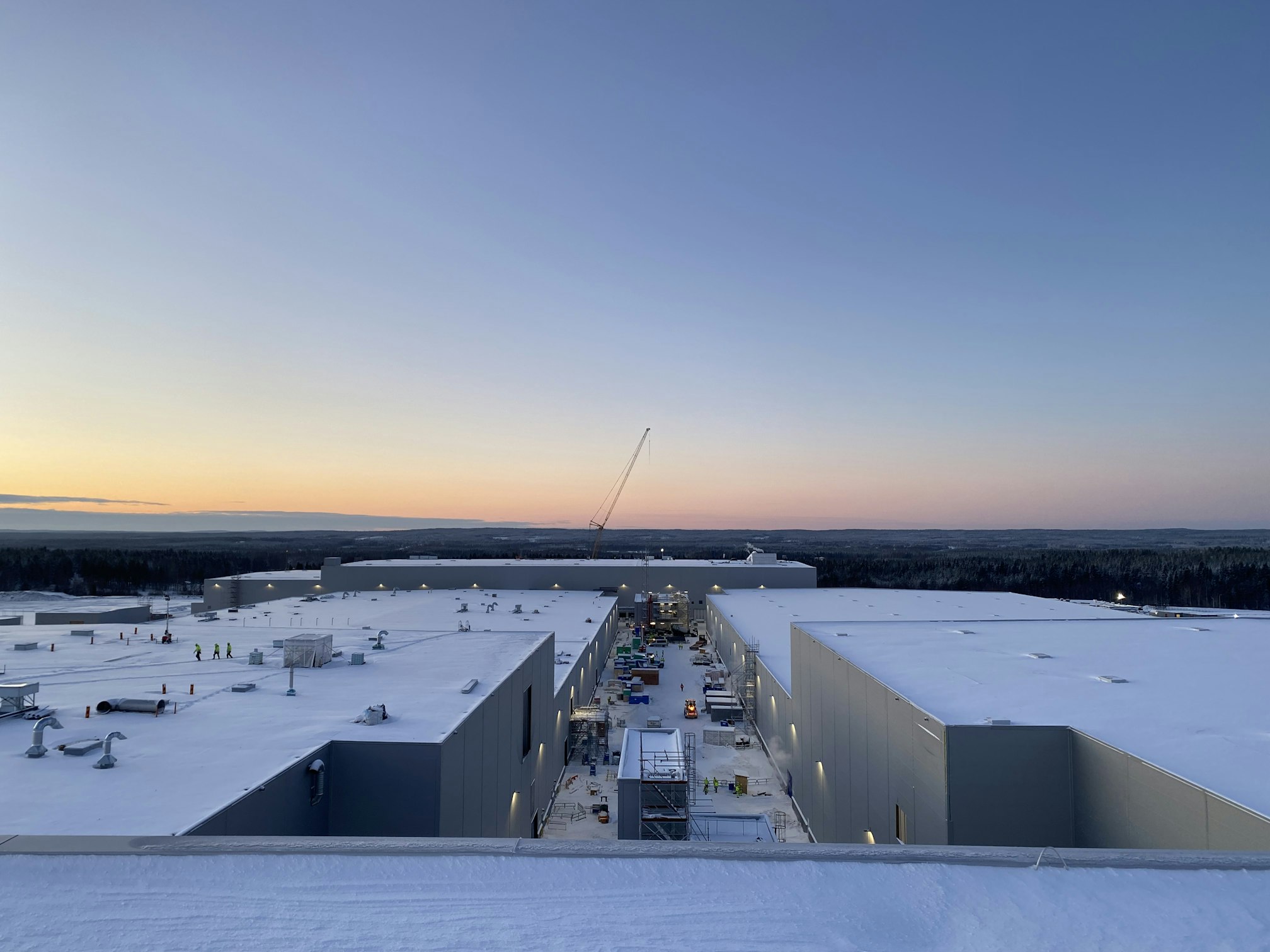
Northvolt Ett is a battery gigafactory. It receives raw metal materials and yields lithium-ion battery cells. Manufacturing a battery from scratch in this way relies on chemical processes to produce electrode material. This initial upstream phase is something most cell manufacturers customarily outsource by procuring electrode from third parties.
Motivated by an ambition to demonstrate a new, more sustainable approach to battery manufacturing, at Northvolt we choose a different path by integrating upstream activities into our own operations. Foremost amongst the reasons for doing this was to ensure that these chemical and energy-intensive processes would be undertaken in a manner as environmentally sound as possible.
To begin with, we’ve located upstream production alongside cell production at Northvolt Ett – enabling use of one of the cleanest energy bases in the world to power the high-temperature processes. At the same time, we’re eliminating the carbon footprint associated with transcontinental freighting of material from traditional electrode producers in China, South Korea or Japan.
Beyond this, owning upstream allows for control over chemical processing itself. This includes bringing immediate transparency on precisely what raw materials are going into Northvolt batteries and where they’ve come from. The approach also brings control over design of electrode material – something which has a decisive bearing on final battery performance.
What this kind of vertical integration of upstream production into Northvolt’s activities has also enabled is a determined approach to designing for circularity of byproducts within the production setup.
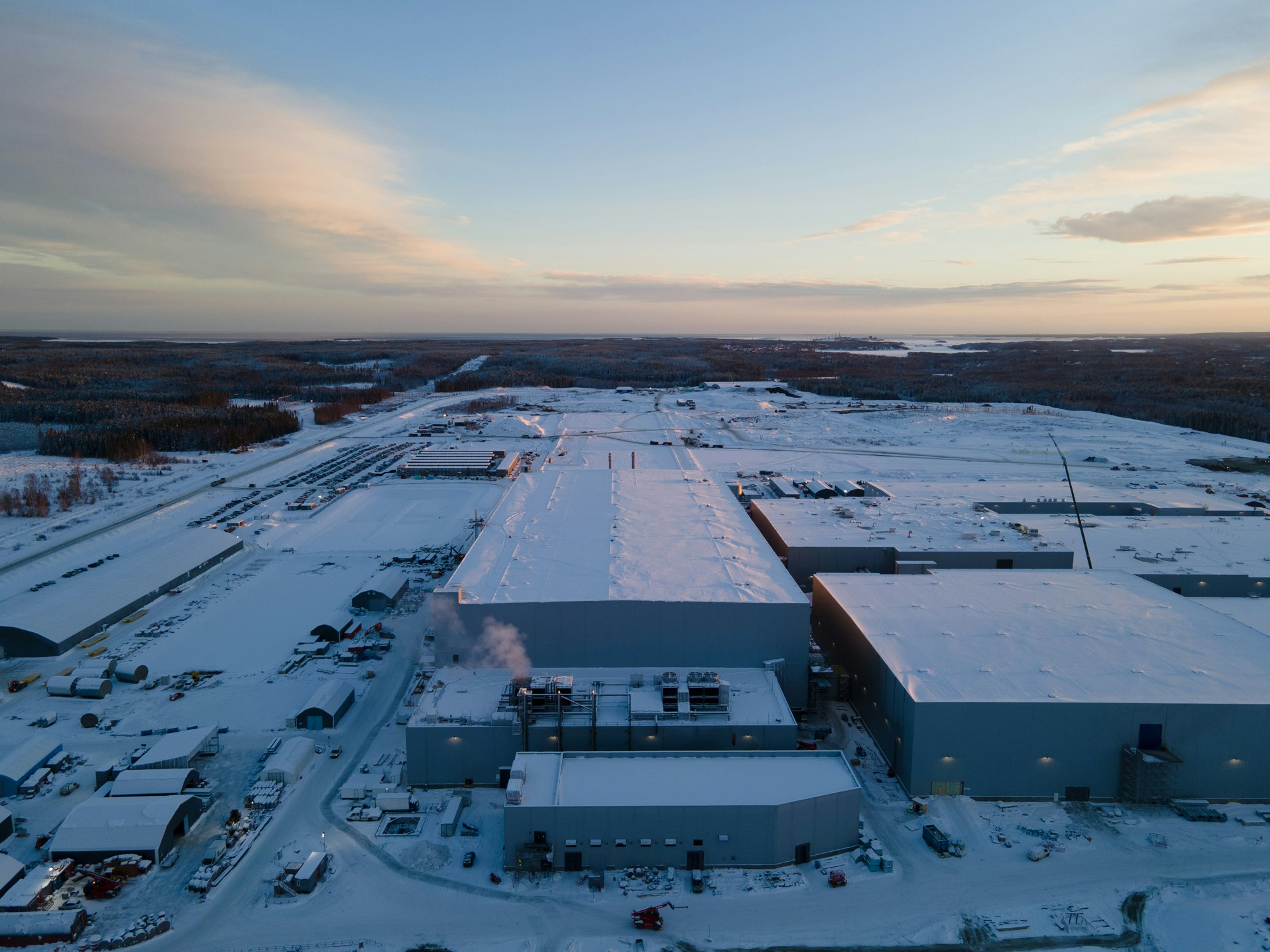
Turning problems into opportunities
At Northvolt Ett the majority of chemical processing is upstream, where we produce active cathode material – a substance containing nickel, manganese, cobalt and lithium. The mixture goes on to be treated at high temperatures, dried and filtered to create a fine powder which is layered onto aluminum foils to create cathode electrode.
The production process involves sodium hydroxide and ammonia, and results in several byproducts which many might view as waste requiring disposal. At Northvolt, the byproduct isn’t regarded as waste at all, but as a resource. Such as it is, the material is full of value and can be recirculated into production processes on-site at Northvolt Ett.
To accomplish this, the byproduct is piped to a treatment plant integrated into the upstream production facility, where we’re isolating, purifying, and recovering three materials: ammonia, a particular kind of salt, and metals.
For ammonia, the recovery process – referred to as ‘stripping’ – involves using steam to pull the ammonia out from the water. With this about three cubic meters of ammonia can be recovered every hour. The recovered ammonia is recirculated into the production process and reused – resulting in minimal requirements for fresh ammonia and avoiding the need for off-site handling of the ammonia.
The recycling of salt is slightly more complex than it is for ammonia, but the outcome has more than justified the investments that were required. The salt being recovered – sodium sulfate – is produced in many industrial processes, but unfortunately the typical industry practice is to flush the salt into rivers and seas as waste. Choosing another direction, at Northvolt Ett the same treatment plant recovering ammonia also reclaims and cleans the salt such that it can be upcycled as a commercial product.

At full upstream capacity, Northvolt Ett will recover around 200,000 tons of sodium sulfate salt each year. That’s a lot of salt… prompting the question of where to send it. A solution was found in partnering with Cinis – a Swedish start-up aiming to produce the world’s most environmentally friendly mineral fertilizer by recycling industrial waste products. With a novel manufacturing setup, together with salt from Northvolt Ett, Cinis’ ambition is to produce a fertilizer with a CO2 footprint 75% smaller than that of traditional fertilizers.
Looking to scale up production, over the next four years Cinis will build two fertilizer factories in northern Sweden, both powered entirely by renewable electricity – one in Örnsköldsvik and another right next to Northvolt Ett gigafactory.
Once salt and ammonia are recovered, a mixture containing nickel, manganese and cobalt is isolated and sent for treatment at Revolt Ett recycling plant, situated alongside the gigafactory. These metals – together with battery scrap and end-of-life batteries being processed at the plant – will be recycled and recirculated into the production of new batteries. Fully built, Revolt Ett will be the largest battery recycling plant in Europe – capable of handling some 125,000 tons of battery material every year to support Northvolt’s target to source 50% of raw material demands for fresh battery production from recycling by 2030.
With ammonia, salt and metals now removed, at the upstream treatment plant all that remains is water, the large majority of which will be recirculated in a closed-loop fashion to the early stages of active material production. Just a small fraction of the process water will be delivered back to the local river at natural temperatures.
The approach described here might sound simple enough. Or perhaps appear like the obvious thing to do. Unfortunately, however, it isn’t standard practice. Instead, it is a deliberate decision to engineer and embed circularity into an industry which would otherwise consume vast volumes of resources.
Current laws might permit the flushing of sodium sulfate into rivers and it might sometimes be easier to send ammonia away for disposal. But if we’ve learnt anything from the climate crisis, it’s that the established way of doing things has to change.
Industrial groups – perhaps especially emergent ones like Northvolt – have a clear and significant role to play in pioneering new standards for industry. And that’s exactly what we intend to do.