Manufacturing a Paradigm Shift
18 February, 2019
The landscape of Li-ion battery manufacturing
We are faced with an unprecedented pipeline of lithium-ion battery factories. The extent of financing, vast physical scale and in many instances sheer complexity envisioned for these facilities based around next-generation, automated technologies is all impressive. But the extraordinary nature of the emergence of these so-called battery megafactories – a term coined by Benchmark Mineral Intelligence in 2014 – becomes most clear when viewed through a lens of historic and current global Li-ion manufacturing capacity. Only when considering this larger context in which their emergence has taken place does the rationale behind megafactories, and indeed their genuine significance, become apparent. After being introduced by SONY in 1991, Li-ion battery chemistry came to prominence in the early 1990s when it rapidly rose to become the go-to battery for consumer electronics. That hasn’t changed, but while the consumer electronics market has of course grown massively over the last few decades, up until quite recently the market demand for Li-ion cells was relatively small.
By 2010, global Li-ion market volume reached little over 20 GWh, with only a few gigawatt hours of that volume being delivered towards anything other than the consumer electronics sector (EU Commission Joint Research Centre, December 2018). Li-ion battery demand from the consumer electronics sector has risen only modestly since then – a trend pitched to continue in the coming decades.
Quite simply then, historic, current and forecasted Li-ion demand for consumer electronics are a drop in the ocean considering megafactory capacities detailed above.
And yet, global manufacturing capacity of Li-ion cells for EVs and stationary storage is currently around 150 GWh according to EU Commission Joint Research Centre. With two-thirds of the capacity being located in China, just 4.21 GWh of that capacity is based in Europe.
The sudden rise in Li-ion manufacturing since 2010 can be traced to the emergence of a wholly new market for Li-ion batteries: electric vehicles (EVs). Around the same time, we also began to see lift-off for renewable energy; bringing with it another new industry into which batteries would play. The field was set for change.
Paradigm shift
As we entered the 21st century, we did so with growing awareness of the need to change our ways. The increasingly apparent consequences and outlook on the impact of climate change resulting from a world fuelled by a diet of fossil fuels presented a bleak and nightmarish future.
There had to be a wholesale change. And if that change was to be successful, it had to happen within some of the world’s largest industries. The deployment of renewable energy systems to deliver clean electricity and heating is arguably the most obvious component in the transition to a decarbonized energy system. Altogether the sector accounts for a little over 40% of our emissions – the largest single share.
With transportation responsible for around 25% of global emissions, the electrification of transportation by land, air and sea is also critical and cannot come soon enough.
While the enormity of the challenge that faces us in decarbonizing these sectors is great, the good news is that we know the path to take. One could even argue we are on our way, armed with many of the solutions we need. To be sure, we are in the early years of this green transition, but we may be reassured by the successes had to date and the fact that the pace of deployment of solutions is exponential.
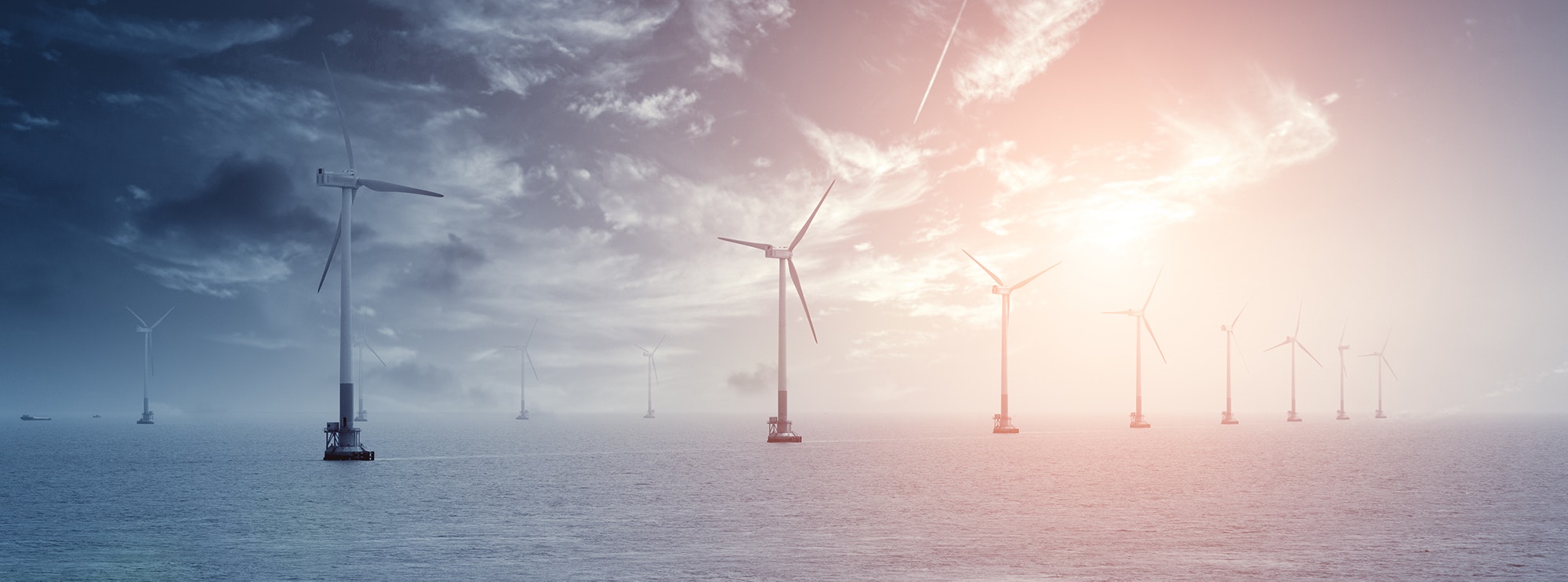
The role of batteries in the early 21st century
Across this new landscape, batteries have a critical part to play. In electric vehicles, whether passenger cars, buses and trucks or heavy industrial vehicles, the function of batteries is self-evident: providing means to power a vehicle (ideally using cleanly-generated electricity).
Since 2010 we have witnessed an exponential rise in EVs hitting the roads; vehicles demonstrating that electrification doesn’t mean compromising on performance, safety or comfort.
There were well over 4 million EVs on the road by the end of 2018, 1 million sold in 2017 and over 2 million sold in 2018 (IEA, BNEF). The trends are clear. And with virtually all EV manufacturers favouring Li-ion battery chemistries, demand has grown massively. (A useful rule of thumb is 4 GWh represents the equivalent to 100,000 medium-sized EV batteries of 40 kWh.)
The role of batteries in relation to decarbonizing the grid is, in places, more nuanced.
Transitioning to a decarbonised renewable energy system necessitates energy storage solutions at a fundamental level. There are many and more reasons for this, and no end to technical details to jump into. But at the broadest of levels, storing energy generated from renewables enables us to overcome the disconnect between generation and demand.
That the sun doesn’t always shine and the wind doesn’t always blow means that we cannot guarantee supply in a fully wind and solar power dependent system without some kind of energy storage.
By storing excess power when generation is high, or when there is surplus, we’re able to shift its use to a point later in time when it’s needed. Essentially, energy storage is the answer to the problem of renewable power generation being intermittent.
“A battery will do for the electricity supply chain, what refrigeration did to our food supply chain.” Professor Donald Sadoway, MIT Materials Science Energy storage also enables certain services to the electricity grid (so-called ancillary services) which are vital to keeping the grid stable. Because renewables are inherently variable in generation, and fluctuating in output, without appropriate measures, important grid parameters such as frequency can deviate away from what’s required. In this respect, energy storage wasn’t required in the past because conventional thermal power generations systems could simply be operated as we needed, ramping up and down to meet demand.
What’s important to recognize is that there is a growing need to deploy effective energy storage solutions (and increase storage capacity) as we increase the share of renewable power generation on the grid, and as electrification, of transportation and other sectors, leads to increasing grid load.
Within these circumstances, battery storage represents one of the most immediate, flexible and well-rounded energy storage solutions. There are other forms of energy storage of course, and to be sure several have a role to play moving forward owing to their particular technical characteristics. But for all intents and purposes it is batteries – specifically of the Li-ion variety – that are pitched to meet our needs.
The shape of things to come
Only in the last few years has battery storage begun to be deployed across the grid at anything like significant scale. Nevertheless, it is most certainly the case that what we are seeing today is the shape of things to come. On all continents we are seeing battery systems deployed in homes, in corporate and industrial settings and alongside utility-scale wind and solar parks to maximise our use of renewable power generation and support the grid in the process.
The vast majority of battery storage deployed as stationary grid capacity in recent years has been based around Li-ion batteries – a trend that isn’t set to change any time soon.
The forecasts for these sectors point to one clear fact: we’re going to need a lot of batteries.
Northvolt understands that battery demand for stationary energy storage systems could grow to 290 GWh by 2030, but potentially much more. At the same time, we’re looking at growth in battery demand for EVs to over 2,300 GWh by 2030, and demand for other industrial and portable applications growing to some 74 GWh by 2030.
It is with this background on a paradigm shift in power and transportation industries that we can explain the jump in global Li-ion manufacturing capacity to 150 GWh according to EU Commission Joint Research Centre.
A call to action
The global industrial response to the circumstances outlined above has been swift and decisive; manifesting most tangibly in the dramatic uptake in planning of new Li-ion battery megafactories.
It was of course Tesla’s Gigafactory which first caught the world’s attention with its scale and ambition. Indeed, its very name, Gigafactory, has become almost synonymous with these monolithic Li-ion battery megafactories. But Tesla is now far from alone. A number of battery megafactories are under development – all tooling up to bring about a cleaner future.
As of January 2019, Benchmark Mineral Intelligence’s Li-ion Battery Megafactory Tracker shows 68 megafactories (rated ≥1 GWh/year) in the pipeline, with a total capacity of 1.45 TWh by 2028. For comparison, the group also report that in 2015 only three such plants were planned. Bloomberg New Energy Finance (BNEF) estimates that global annual investment in the Li-ion battery market by 2024 will be approximately $13 billion – more than twice the $5 billion annual investment of 2018.
Altogether, BNEF estimates $61 billion will be invested in the Li-ion cell market between 2017 and 2024.
The European pipeline is considerably smaller than that of Asia – the historical cradle of battery manufacturing – but it’s pitched for growth. Multiple megafactories are now under development in Europe, and the continent is on track to increase manufacturing capacity by twenty times in the next seven years, according to Wood Mackenzie Power & Renewables, which forecasts annual output of 90 GWh by 2025.
The European pipeline includes LG Chem’s plant in Wroclaw, Poland, which has announced ambitions to ramp up to 70 GWh in the coming years – a move that would cement its position as one of the largest megafactories in the world.
Bloomberg have reported that China’s CATL will establish a foothold Europe too, with a new megafactory in Erfurt, Thüringia. Recently it was reported that CATL seeks to reach an annual output of 60 GWh by 2026. In March 2018, SK Innovation held a groundbreaking ceremony for its first European Li-ion battery factory, located in Komárom, Hungary. Production is slated to begin early 2020, and once all the production lines are installed, annual capacity will reach 7.5 GWh.
Northvolt is another player on the scene. We’re building Northvolt Ett (meaning One in Swedish) – what will become one of Europe’s largest Li-ion battery factories, in Skellefteå, some 760 kilometers north of Stockholm, Sweden.
Construction of the factory began in June 2018 and the first 8 GWh/year block will be operational in 2020. Ramping up to full capacity, we’ll reach 32 GWh/year. In so doing, we’ll establish substantial new domestic battery manufacturing capacity for Europe – something which in itself carries great strategic significance for the European Union.
Northvolt Ett’s first block will cover 170.000 square meters, but the complete factory we sprawl out over more than 500.000 square meters of subarctic land – an area larger than the Vatican.
There is much at stake in this enterprise. Aside from supporting the paradigm shift outlined above, a European battery supply chain would bring millions of new jobs according to InnoEnergy, security of supply for a product pitched to fulfil a pivotal role in future energy systems, and a market valued at up to €250 billion a year from 2025 onward, according to the European Battery Alliance.
The rationale for building at scale
With battery megafactories, size is not simply a reflection of future demand for Li-ion batteries. This is of course a major driver for their design; after all, with scale comes sheer manufacturing output. But a more accurate reasoning for building at such scale is to be found in the notion of economies of scale.
When we produce anything, from paperclips and bottles to more complex products and systems such as mobile phones or aircraft, manufacturing in large volumes has the inherit outcome of reducing unit cost. This is most keenly evident in the history of the semi-conductor industry, which went through a dramatic rise in manufacturing capacity through the 1990s to keep pace with demand as we moved into the digital age.
With battery cells, the situation is such that while initial start-up costs for cell manufacturing plants are very high, the economics of several key manufacturing process steps, especially in electrode production, scale up very nicely. With larger manufacturing lines, we can leverage this principle to reduce costs significantly – meaning that the first MWh capacity is considerably more expensive than subsequent ones. Applied over much larger scales, the economic returns change the dynamics of cell manufacture entirely. In some instances twenty-fold gains in process efficiency can be found in scaling up from a conventionally sized manufacturing plant to a megafactory.
Additionally, a larger facility can be operated more energy efficiently than several plants of the same cumulative capacity. This is important, because battery cell production is an unavoidably energy intensive process.
This model of large-scale cell production represents a fundamentally new approach to battery manufacturing. Altogether this evolution will be key to optimizing processes, reducing costs and gaining greater flexibility in how we design and build cells, packs and modules. A reduction in unit cost is key, because for all we have seen deployment of stationary energy storage and adoption of EVs, the future we envision relies on significant cost reductions of batteries.
A looming supply gap and the work ahead
For all that this global push for battery megafactories might lead one to believe we’re surely going to have enough batteries for the future, there’s a twist in the tail – it’s not enough.
Even conservative forecasts of future Li-ion battery demand make for startling reading, revealing that expected market demand towards 2030 will likely outpace supply based on current projections of global manufacturing capacity.
Noting that Benchmark Mineral Intelligence’s latest figures pitch a total manufacturing capacity of 1.45 TWh in 2028, battery demand for EVs alone could grow to over 2.3 TWh by 2030. Projections from the EU Commission Joint Research Centre suggest that by 2040 global annual sales of Li-ion batteries will increase to around 2 TWh in a medium scenario and 4 TWh in a high scenario.
The truth of the matter is that we’re going to need many more battery megafactories. All the more reason, in our view, that we establish sustainable approaches to the sourcing, production and recycling of batteries.
The battery megafactories we see rising around the world today represent far more than technological might and innovation. They reflect global industrial adaptation necessitated by a world seeking a cleaner future. That adaptation won’t happen on its own, but it is absolutely essential that we secure it if we are to have a fighting chance against the worst of climate change.