The Northvolt–Volvo Cars joint venture: a holistic approach
7 November, 2022
In June 2021, Northvolt and Volvo Cars joined forces to build the next generation of pure electric Volvo cars. A shared commitment to safety and sustainability provided a firm foundation for the partnership. But what will this look like in practice? Here’s an explainer on the Northvolt-Volvo Cars joint venture.
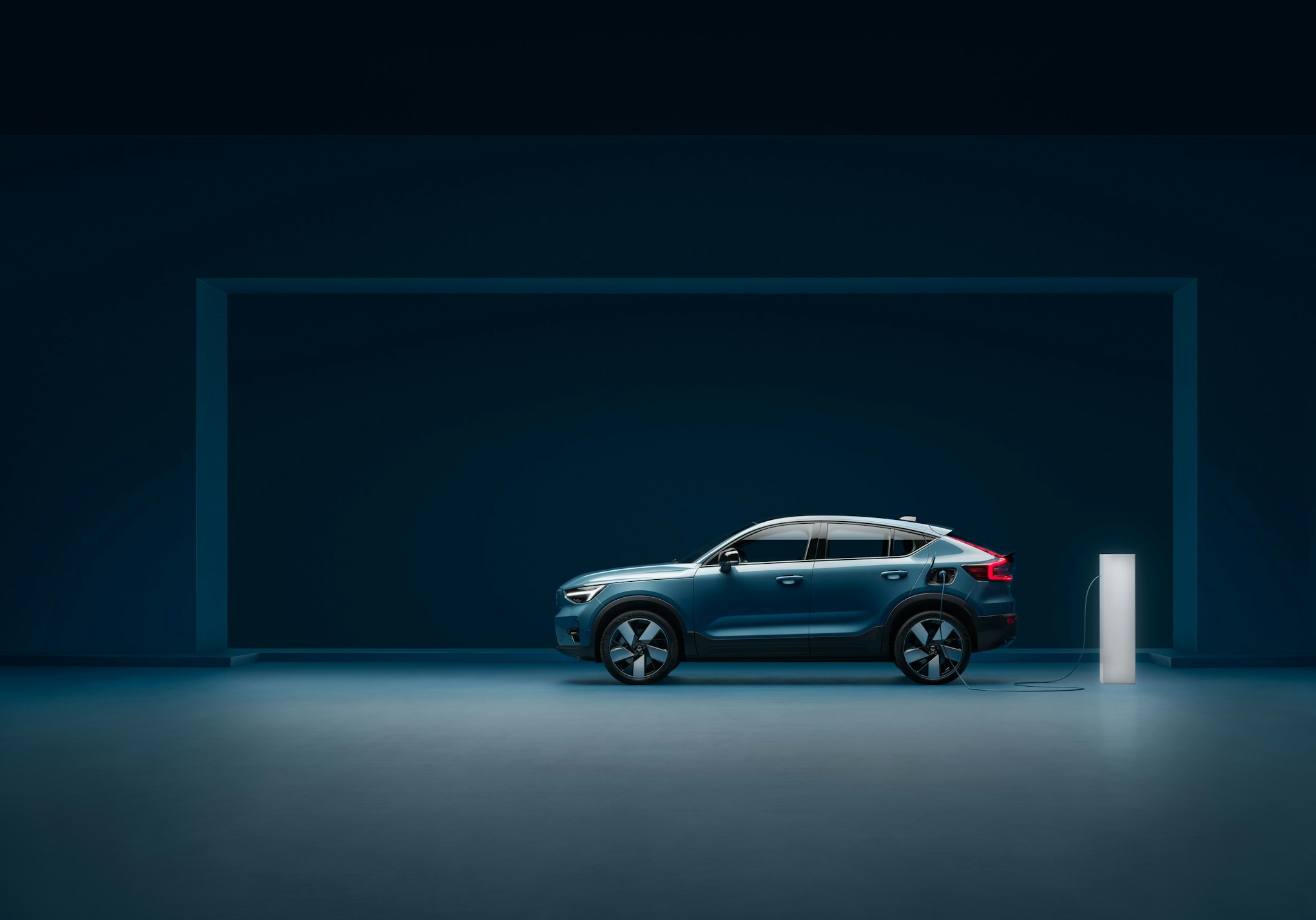
Volvo Cars aims to become a fully electric car maker by 2030. For this goal to become a reality, completely embracing battery technology is key. This is where the joint venture comes in.
The joint venture will enable collaboration across the entire battery technology space, from research and cell design all the way to production.
The JV is divided into two parts: Research & Development and battery production. R&D will test new technologies to design the best possible cells to meet Volvo Cars’ product needs. These cell designs will eventually be handed over to the production side of the venture. Here they will be produced sustainably through the joint venture’s battery gigafactory under development in Gothenburg.
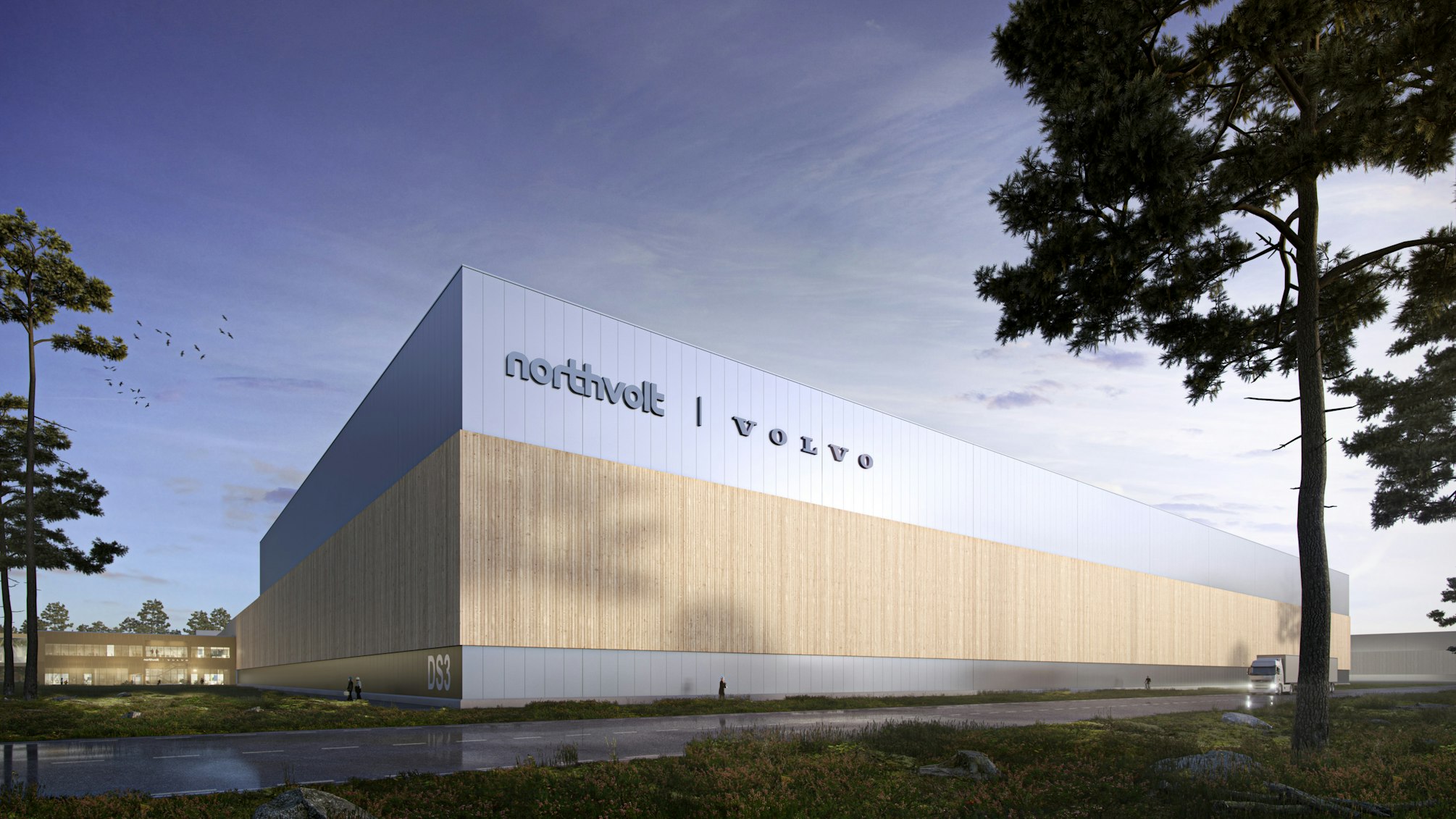
Why join forces?
By creating a fully integrated and frictionless environment, the JV will facilitate the development of new battery technologies.
Eerik Hantsoo, Chief Technical Officer of the joint venture, explains:
“The future of vehicles is electric, and batteries determine almost everything about EV performance. Because of how strongly batteries drive vehicle performance, you can no longer procure batteries the same way you would a windshield wiper."
Eerik highlights how the joint venture enables a far-sighted and holistic approach to designing, manufacturing and finally integrating batteries. In this way, battery technology is positioned more as an extension of vehicle design, and less of a stand-alone component.
“Working together through the joint venture allows for a closer collaboration on battery design and integration into the vehicle than is more meaningful than a simple business transaction.”
This is a long-term relationship
In practice, this means that Volvo Cars and Northvolt will share influence over the entire development process – a dynamic that opens new opportunities to innovate and improve the battery, and, ultimately, the vehicle.
Eerik suggests this is especially important in terms of sustainability, supply chain and cost:
“There are some design features that can be added to a cell, which may make cell production more expensive, however, once this cell is built into a vehicle, the total installed cost may be lower.”
“By working closely with Volvo Car's design team, we hope to find ways to decrease vehicle-level complexity and cost, even if that means adding some complexity to the cell,” says Eerik.
The JV will also leverage the opportunity to design for sustainability upfront. Eerik suggests that a good example is designing the cells in ways that make them easier to remove from the vehicle at end-of-life and more amenable to efficient recycling.
“Northvolt lives and breathes making sustainable batteries and enabling the transition to electric without doing more harm than good. That's clear to the whole world. Northvolt and Volvo are in complete agreement about sustainability.”
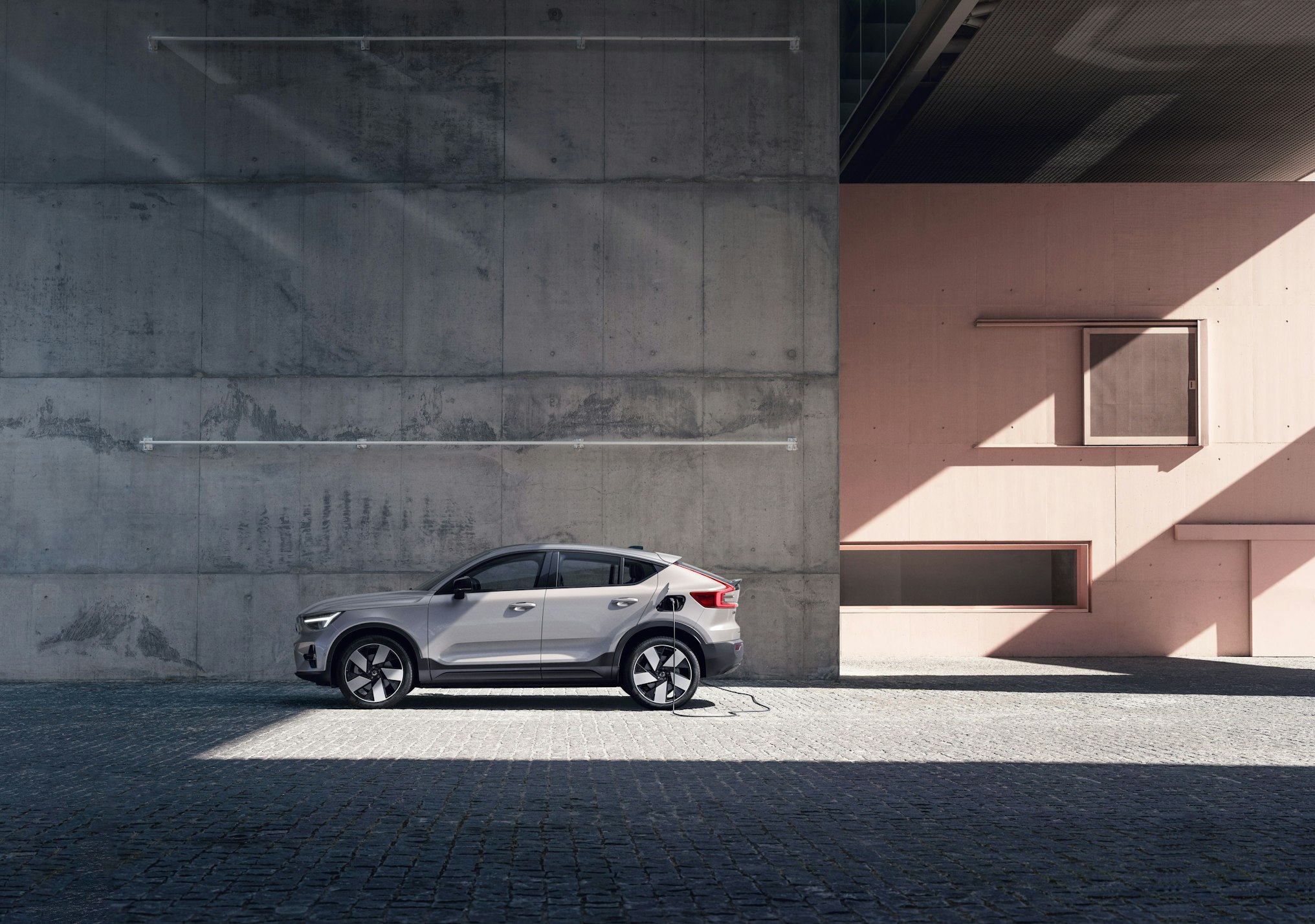
Tailor-made batteries
Like any EV manufacturer, Volvo Cars has some key characteristics that they desire from their batteries. Specific to the Volvo brand is an emphasis on safety, as well as cold weather performance. The JV is able to adjust R&D and production processes to place an extra level of focus on these particular characteristics.
“Volvos are safe, so the cells that we put into them need to live up to Volvo standards of safety, which are extremely high,” says Eerik, describing how the JV will be investing in temperature chambers, that simulate particularly punishing thermal conditions over a longer period of time.
Additionally, like most automakers, Volvo Cars aims to improve the energy density and fast charge capability of their batteries. By having an in-house R&D facility, the JV can focus on these key characteristics through parallel workstreams. One workstream would focus on optimizing energy density, and the other would aim to improve fast charge capability.
The leading technology from each workstream will be integrated into a cell design that meets Volvo Cars’ specific requirements for a certain vehicle. Eerik hints that in the future, additional workstreams will be introduced, including ones focused on longer-term technology development.
This collaboration creates space for innovation, and for testing out different avenues in order to achieve the best results possible.
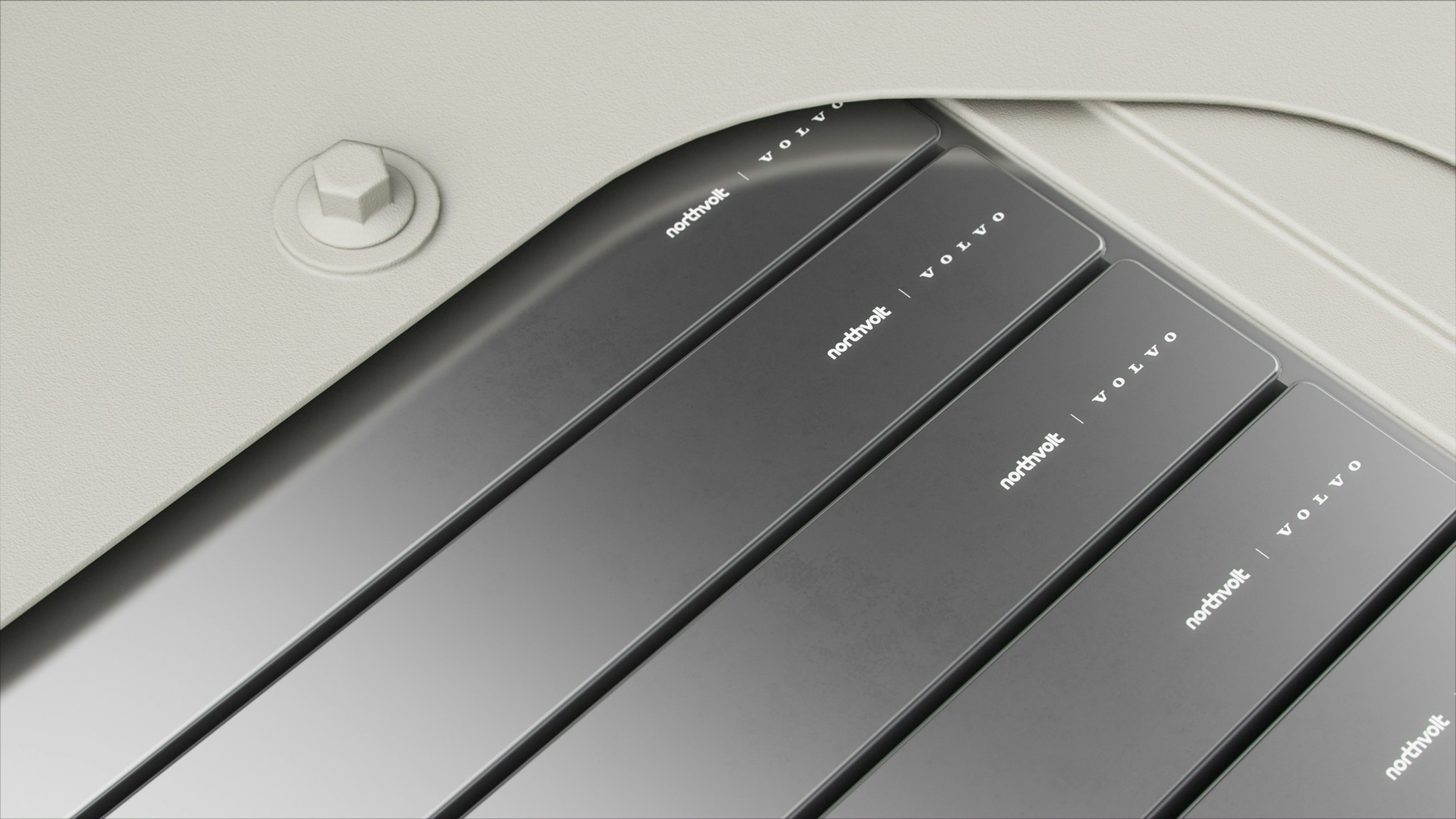
The future of the JV
Work during the first year will focus on growing the team and setting up some essential functions. The most essential function is the internal cell build, which begins with coin and single layer pouch cells:
“We are starting with smaller batteries. One of the benefits of starting small is that we don’t have to wait for a complete production line to be up and running. We can start early.”
In the next five years, the JV plans to take the design of the small battery developed over the first two years and scale that up into a full-size battery.
“As we scale up the organization and can do more experiments, we are going to be ramping up some efforts in other areas that are of strategic importance to Volvo Cars. Northvolt has been massively supportive of us, as we're getting ourselves up and running. That cooperation is exceptionally valuable to us.”
Want to work at the Northvolt-Volvo Cars JV? More info here.