Connected factory: the path to smart manufacturing
28 January, 2021
A connected factory is one we can better understand. And that means better, safer cells, and a surer roadmap to deploying more manufacturing capacity.
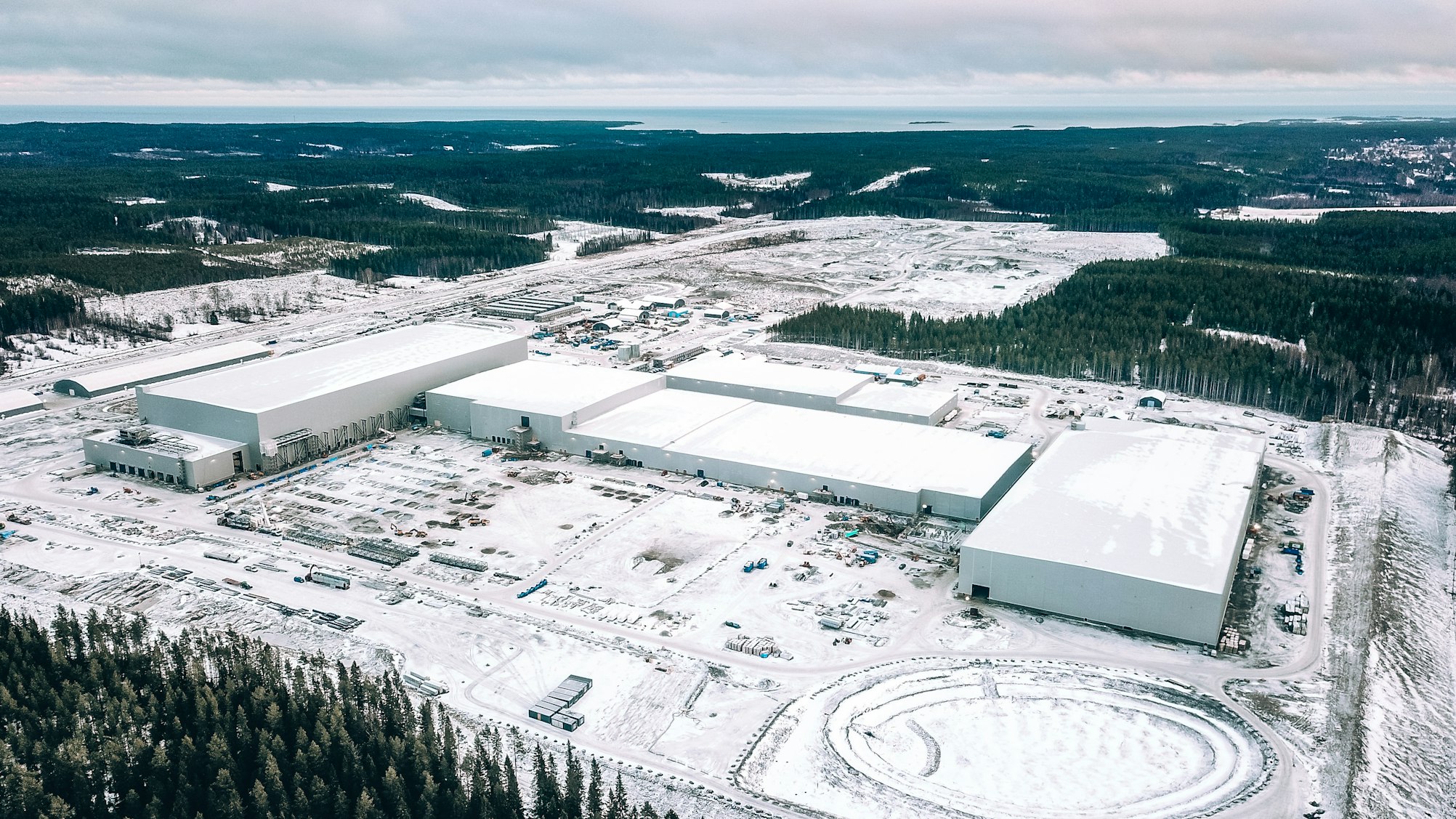
The setup
Consider the following scenario: you’re tasked with establishing a Greenfield factory with an output in the order of billions of units per year. Despite the high volumes in play, you’re not dealing with a commodity item, but instead, a product that’s as sophisticated in design as it is complex in manufacture.
Both customers and relevant authorities alike require the highest standards of quality control throughout the manufacturing process; along with insight on the material contents of each unit, which you’ll be producing from base raw materials.
While the scale of the factory is daunting, one aspect of its design is to your benefit: the 500,000 square meter footprint will include five 300-meter-long, 100-meter-wide manufacturing blocks which, more or less, are copies of one another.
Final point: establishing the factory, you should be mindful of intentions for deploying several more factories of similar scale and design in the coming years.
The response
It was essentially this scenario that was to play out in developing Northvolt Ett lithium-ion battery factory in Skellefteå, northern Sweden.
With the commissioning of the first production lines later this year, it’s fine timing to present insight on a key aspect to the approach that was taken in establishing Europe’s first gigafactory: a clear embrace of digitalization – one characterized by high levels of data collection and usage, and process automation.
From the outset of planning Northvolt Ett, the motivations for adopting a digital approach could be considered over two dimensions: production capacity ramp-up and operations.
Relating to capacity ramp-up, digital solutions promised a streamlining of the deployment of production lines and minimizing of delays in reaching target efficiencies of machines, lines and the factory as a whole.
Within operations, digitalization could be leveraged to support activities in and around production, including maintaining and extending the efficiency of production lines, reducing material and resource consumption, and assuring product quality.
But the solutions required wouldn’t appear overnight. There is no plug-and-play digital toolbox, no turn-key solution for embedding Industry 4.0 into a battery gigafactory. A pragmatic, stepwise approach was required.

Step 1: Connect
Connecting a battery factory is easier said than done, but it’s the foundation for everything else. We need to network hundreds of machines and thousands of process components within the equipment to collect data from every source possible. At the very least we require machine settings, real-time operating performance data, and broad-spectrum information on the material it’s handling. The next challenge is to develop software to integrate data and build platforms to present it in such a way that it’s actually meaningful and usable to stakeholders – production technicians and operators, maintenance teams, factory designers, and others.
The data pool at this point is comprehensive. Besides machine data, we’re dealing in rich streams of information collected from material-facing devices as diverse as temperature sensors, thickness measuring beta-gauges, X-ray, high-resolution cameras and positioning systems, all alongside data from the factory itself, such as environmental data of production areas.
The development of necessary software and back-end architecture is undertaken by Northvolt software teams working in collaboration with process engineers, quality control experts, and cell designers with specialist knowledge of how the cells are to be built.
By doing this in-house, we’re securing a customized software solution for Northvolt Ett. At the same time though, we’re fostering competencies that will pay back hundredfold as we move on ambitions to design, deploy and connect additional production lines and plants.
This first step is a tedious one… especially the first time around. Fortunately, the smaller scale of Northvolt Labs in Västerås provided training grounds for this work ahead of the twenty-times larger scale of Northvolt Ett.
Step 2: Leverage
Once we have data, we can begin leveraging it across different operational contexts. Amongst many use cases, some of the most significant are in securing production efficiency, quality assurance and product traceability.
Producing battery cells is so incredibly hard partly because of the extremely low tolerance there is for deviation away from design specification. Microns matter in first sizing and then placing components, milligrams and milliliters matter elsewhere, and surface imperfections on materials – invisible to the human eye – can compromise cell performance and safety.
Reliable, efficient production of quality cells at the kinds of volumes involved at Northvolt Ett, therefore, relies heavily on the collection of high-fidelity data at every step along its production lines, as well as evaluation of cells at the end of production.
An important area of work in this field involves the exploration of which metrics of material and product inspection are especially significant and which less so in the context of determining final material, component or cell quality.
For instance, so-called predictive quality techniques involving analysis of large volumes of data can be employed to avoid further investment of cost, materials or time into the production of something which won’t pass later quality checks.
Closely related to quality control is process control. Here, digital tools are supporting the crucial (traditionally time-consuming) task of calibration of equipment, followed by subsequent and proactive monitoring of machines throughout operations to ensure production lines are operating optimally. This includes routines to ensure that machine downtime is scheduled, and any loss in throughput is balanced and compensated for without creating bottlenecks in other areas of the line.
We can also leverage data to streamline and even automate changes in manufacturing protocols that are required for different cell products being manufactured on lines. Additionally, factory data can be used to support operations beyond the production floor – for instance, understanding material consumption and output of machines in order to better plan inbound and outbound logistics flows.
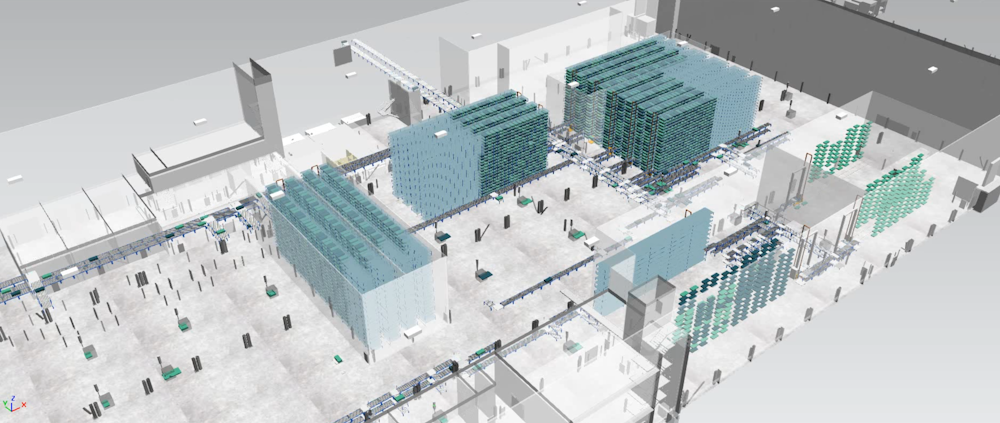
Outcomes
Responding to the urgency we face in needing to scale up battery cell manufacturing capacity to meet the needs of industry, the deployment of many more factories the size of Northvolt Ett is necessary.
In Northvolt’s pursuit of 150 GWh manufacturing capacity by 2030 – which is nothing short of establishing a new supply chain for Europe – recognition of the boundless potential for integrating digital solutions into both design and operation of these facilities is vital.
A connected factory is one we can better understand, quantify and optimize. And that means not only better, safer cells, but also a surer roadmap to deploying more manufacturing capacity.
Full traceability back to the earliest stages of production processes. Precision repeatability of processes for quality assurance. And complete digital twinning of cell production lines and whole factories. These are the kinds of digital tools that will take us to the next level of manufacturing.