Long read: Emission-free, electric construction with mobile batteries
3 November, 2021
As construction industries drop combustion fuel technologies and make the switch to electric solutions, a clear need arises for temporary on-site battery energy storage. Enabling zero-emissions construction, Norwegian energy provider BKK recently deployed a Voltpack Mobile System from Northvolt to show how a battery system opens the doors to cutting out the oil. Here’s what happened.
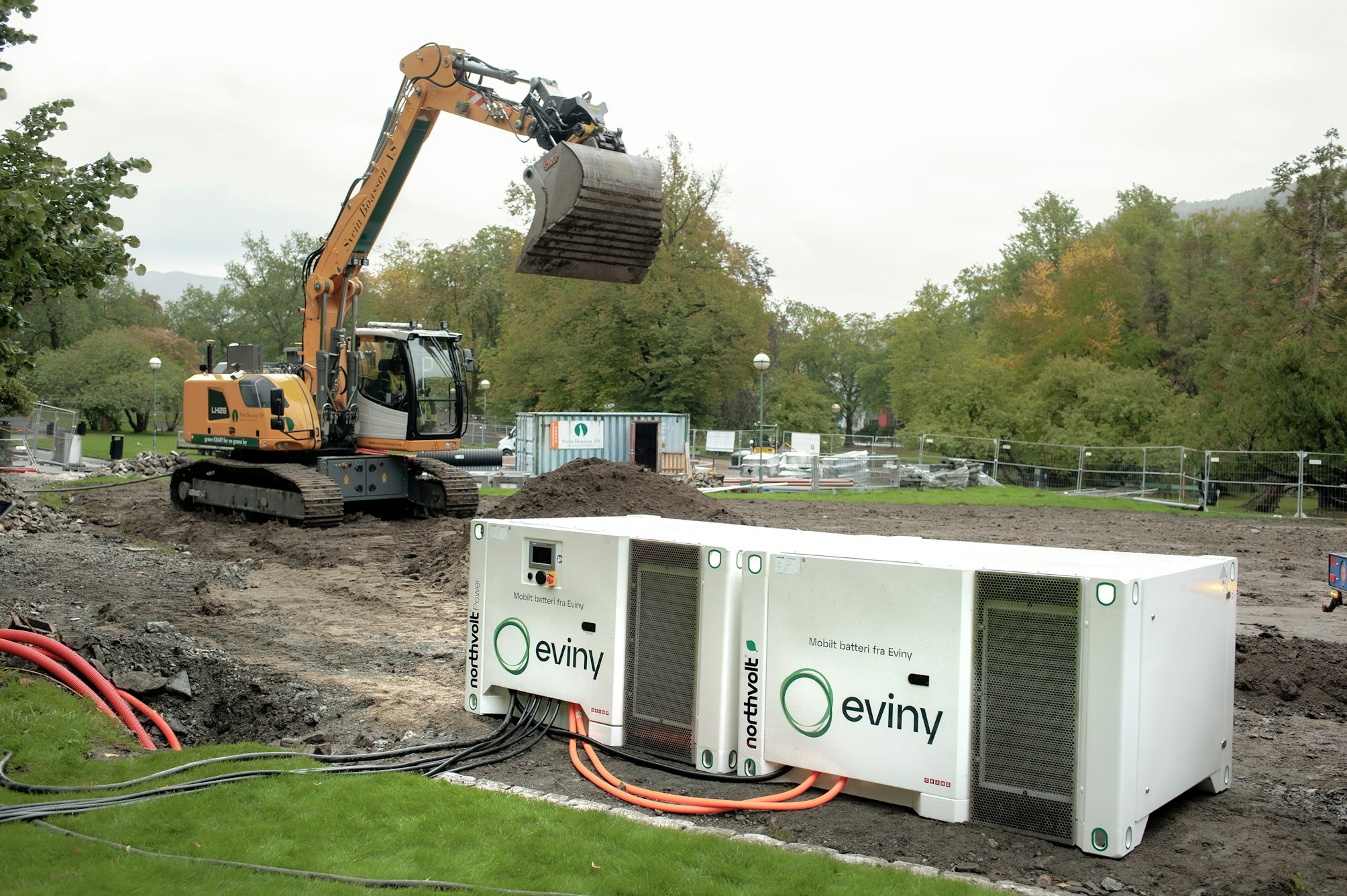
A new kind of construction site
The 26-ton excavator and smaller tractor machine working in coordination, digging trenches in suburban Bergen, Norway, maybe appeared an ordinary sight. But a closer inspection revealed something different. Absent from the construction site was loud noise and the smell of exhaust fumes. This was an electric construction site. And it was a sign of things to come.
“The fact is that there’s a massive change happening in the way that heavy machinery, like construction machinery, is being powered,” Camilla Moster, Leader for Mobile Energy at BKK, tells Northvolt in interview. “Here in Norway, we might be ahead of the curve, but the switch to electric machines is spreading.”
“We’re seeing early-adopters in industry embracing battery electric machines in pursuit of emissions reduction and sustainable operations. It’s a change that requires new solutions to charge and power these machines, but in beginning to deploy these solutions, we’re seeing their value emerge and new opportunities.”
Enabling electric construction
Norwegian energy company BKK is an early customer of the Voltpack Mobile System – Northvolt’s first scalable, redeployable battery energy storage system. In September, the company positioned a 281 kWh variant of the system, which can be scaled to 1,405 kWh, into a construction site outside of Bergen.
The Voltpack Mobile System was used to power an all-electric 26-ton excavator, a smaller digger and a variety of small applications. “This was a 5-day demonstration,” says Camilla, “but the system performed very well and shows what to expect in the future.”
"What was especially great was the quick and simple deployment – we connected and started the system ourselves in only a few minutes. Our end customer was also very happy; with this system they gained the flexibility required and can now plan to use the large excavator also in locations with weaker grid connections."
While the deployment was short, Camilla explains it showcased key capabilities and benefits that mobile batteries bring to construction.
“At the center of the shift we’re seeing is electric vehicles and machinery – compared to conventional diesel variants, these machines dramatically lower emissions associated with a construction project. But bringing electric machines onto site carries consequences and it’s here where batteries play a key role in enabling the transition.”
Illustrating the immediate positive impact of electric machines, BKK report that in the Bergen demonstration, replacing a combustion engine variant that would have required some 10 liters of diesel every hour, with an electric excavator meant avoiding 350 liters of diesel being burnt and 931 kg of CO2 being released into the streets. Scaled up to a 6-year lifetime of operations (around 9,800 hours), the same machine would have released some 1,8 million kg of C02.
“Looking at these kinds of figures, it’s immediately obvious to see that these electric solutions, scaled up and more widely adopted, will have a tremendous positive impact on reducing emissions. It’s exactly this which BKK want to accelerate. Batteries are key to the powering vehicles directly, but what we also see is that the role of batteries in construction goes much further.”
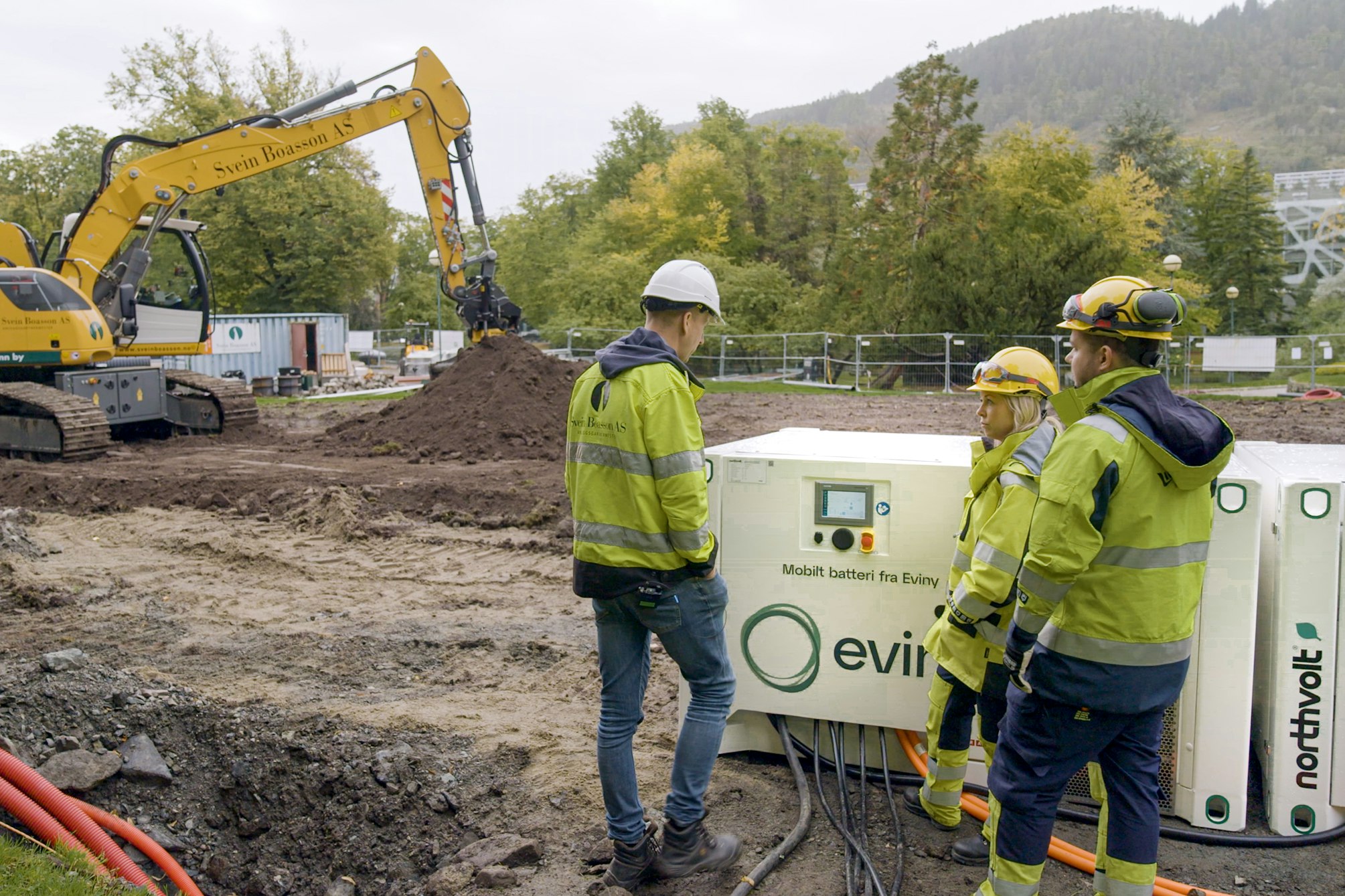
a battery system provides the solution – enabling us to reinforce the grid and increase the power we can make available to site
A sustainable solution for temporary, scalable power supply
One of the challenges with electric machines relates not to the performance of machines themselves, but their charging. And more specifically, how to get power to site.
“Looking at a construction project,” says Camilla, “the largest power demands typically come from excavation and groundworks – work that requires very heavy machinery, requiring a lot of power. And this can be hard to handle via existing connections to the grid, if it’s possible at all.”
“Oftentimes, electricity grids aren’t built to support new power loads being added into their system from a construction project. An additional challenge is that the electricity demand at any given point in time can vary a lot depending on what kinds of operations are being completed, and this kind of fluctuation creates all sorts of additional problems for the grid.”
To this Camilla adds that even where a grid connection does exist, it might not be strong enough to allow for quick, efficient charging of machines. “This is a real drawback – what’s absolutely key for operators is to ensure they have maximum uptime of machines. In other words, for electric machines to be a success, they need to deliver the same performance, when it’s needed, where it’s needed, as the diesel-fueled machines they’re replacing.”
“To all of these challenges, a battery system provides the solution – enabling us to reinforce the grid and increase the power we can make available to site, or even work off-grid entirely. What we’ve now begun to see through our tests is that the solution works.”
With a battery system as a buffer between the site and the grid, operators pull power from the battery system and not the grid itself, thereby keeping the demands on the grid more evenly distributed across the day regardless of the operations taking place.
“This is better for the grid operator, but it’s also advantageous for the construction operator, since the battery can be charged at night when demand is lower and electricity cheaper.”
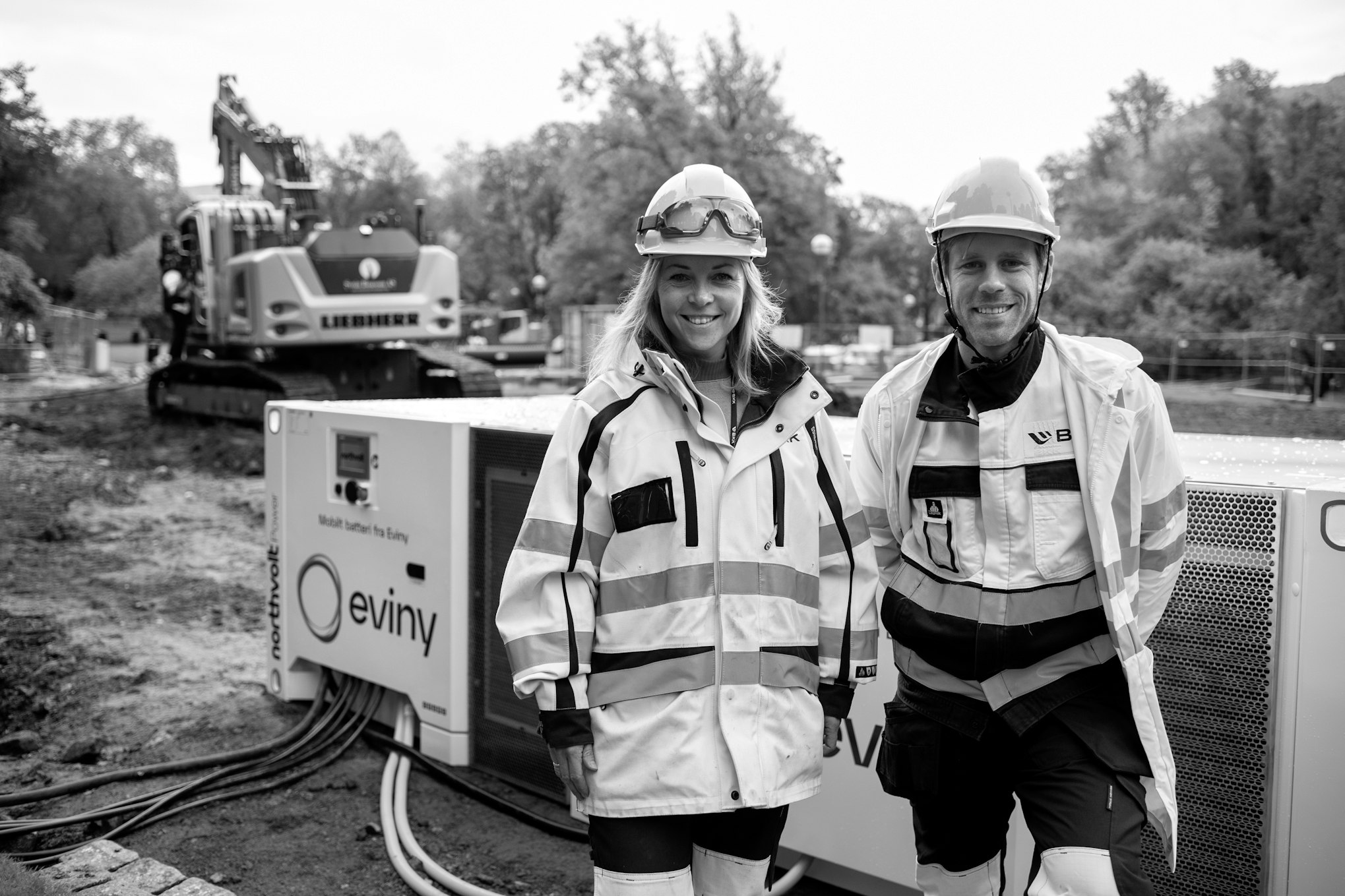
Camilla Moster of BKK with Callum Hoare, Northvolt Systems engineer and manager for Integrated System
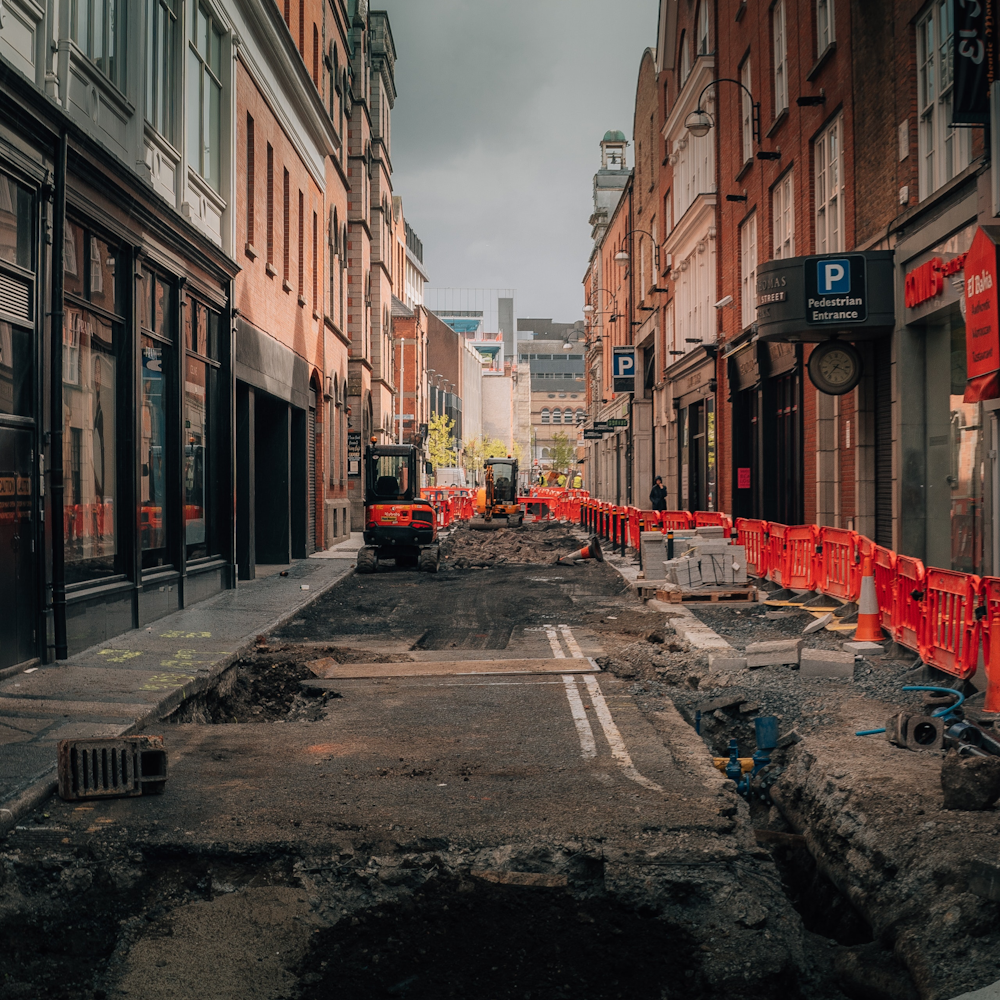
Replacing diesel generators
In the background to powering heavy machinery, Camilla notes that batteries also serve more straight-forward purposes. “On almost any site there is the basic need for powering lighting, heating, general equipment, huts and so on. In many cases a diesel generator is used today to ensure a site has enough power, but it’s not ideal – not least because they’re a direct source of emissions."
"A battery on the other hand, is clean, quiet and easily able to handle these loads, as we saw in Bergen.”
Considering a mass reduction of diesel generators alongside the adoption of electric construction machines, it becomes very easy to see how the construction sites of tomorrow will be very different from those of today.
That the industry is often neglected in the discussion surrounding emission reduction is mistake for this very reason: not only is it responsible for significant emissions, but cleaner alternatives already exist today.
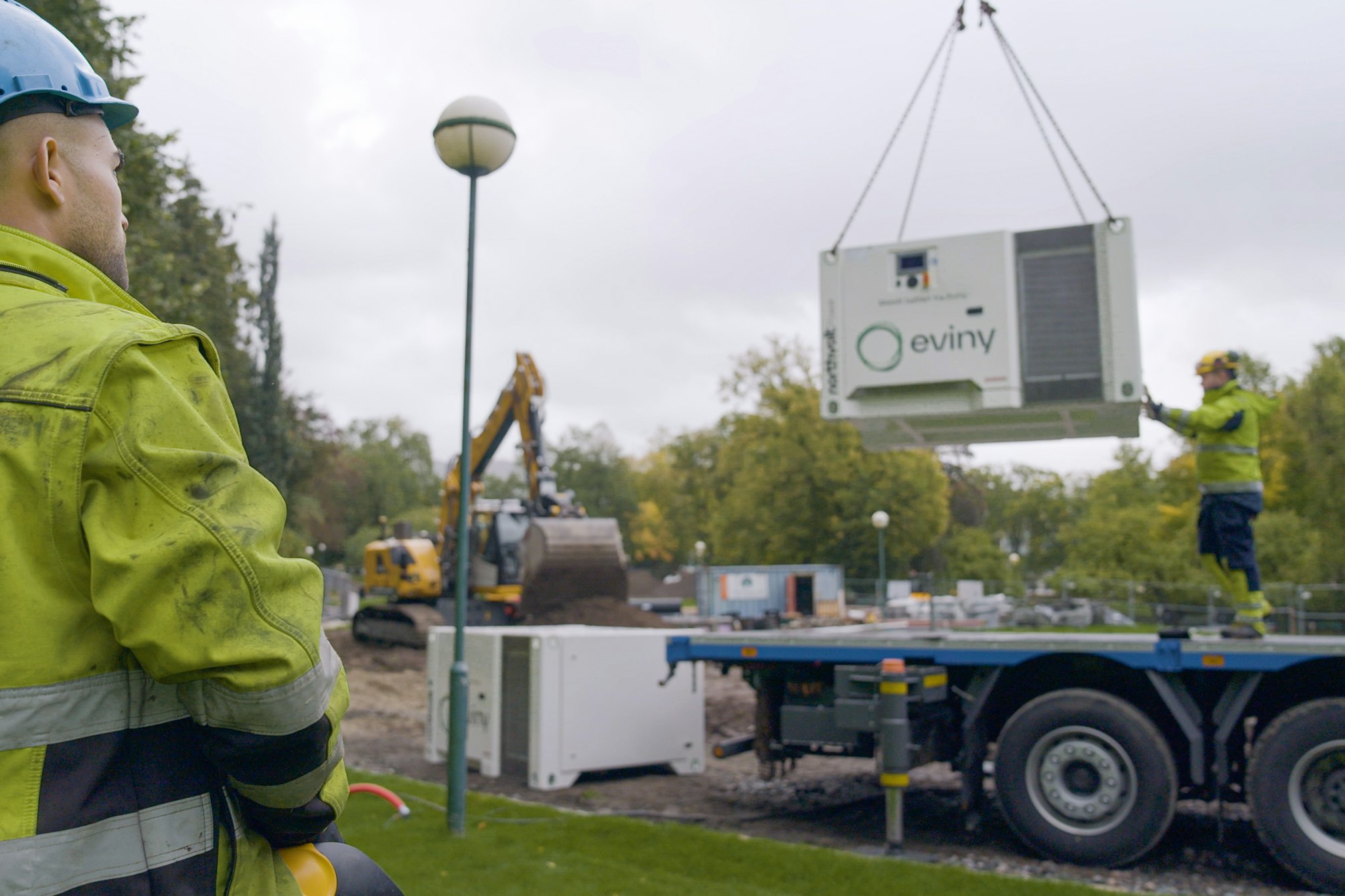
The importance of designing for mobility
Moving beyond the functional role of batteries in electrifying construction, the technology also brings practical benefits.
“I see this in two ways,” says Camilla. “First, there is the way that a mobile battery allows us to power a site on a temporary basis. This is really significant. A construction site needs power, often a lot, but once a project is completed, that need could be gone. For this reason, expanding or reinforcing the grid to connect a site with high power for a short period of time is neither cost efficient or good for the environment.”
“Instead, with a battery system, we can deploy very quickly, operate for precisely as long as is required, then pack it up and redeploy at another location on site, or at another site entirely. Of course, the system needs to be designed for this, and we see that Voltpack Mobile System is – both with its hook-up points for lifting and a robust design that’s needed in construction.”
“Second to this, there are advantages in terms of scalability, meaning that with batteries we can easily deploy capacity as is necessary to support the power requirements of anything from small to large sites, and the varied activities taking place. With Voltpack Mobile in particular, it scales from 281 kWh to 1,405 kWh depending on how many packs we add. At Bergen we tested the 281 kWh configuration, but we’re looking forward to scaling up in the coming months.”
“This kind of scalability is possible due to the modularity of Voltpack Mobile, but it’s also very practical because it means it's much easier to transport, to lift and deploy. When you have a small footprint for the system, as you might often in street construction sites, these details are important.”
“Altogether, the features and design of Voltpack Mobile System were key for us in selecting it. We haven't seen any other suppliers with that kind of functionality and design.”
“A key driver for the project has been to identify how we can avoid costly, unnecessary grid capacity for temporary needs – the Voltpack Mobile System is an ideal solution.”
Towards sustainable construction industry
“At BKK, the mission is to make emission free technology available for everyone, wherever you need it. A key enabler for that is mobile battery energy storage, just like the Voltpack Mobile System we’ve been using in Bergen, Norway. We’re still at the early stage of this transition, and there are certainly challenges, but it’s a bright future. Norway offers a lot of examples of electric machinery in action, but other countries will soon start picking up on this. They have to if we’re to reach climate targets.”
Learn more about Voltpack Mobile System in 'Emission-free construction: Vattenfall’s deployment of Voltpack Mobile System'