Meet Emma Nehrenheim, Chief Environmental Officer at Northvolt
12 March, 2019
Meet Emma Nehrenheim. Professor in Environmental Engineering of Mälardalen University, academic researcher, industry innovator, and now the person charged with delivering the world its greenest battery.
Meet Emma Nehrenheim. Professor in Environmental Engineering of Mälardalen University, academic researcher, industry innovator, and now the person charged with delivering the world its greenest battery.
“I’m an idealist and an environmentalist,” says Emma. “The thing is that when you want to really accomplish something, and you’re in a small corner of the world, it’s hard to make an impact on the larger scale. So when a project like Northvolt comes along, one that’s really going to have a big difference, you jump at that.”
For Emma, that jump came April 2017. Working with ABB at the time, a Sunday morning phone call brought Emma into the office to meet with a new customer — an ambitious start-up that had recently emerged onto the Swedish industrial scene with big plans.
“From that first meeting, I knew I wanted to be involved with Northvolt. The importance of what Northvolt was planning was immediately clear to me.”
Though Emma’s background had little to do with batteries, it had everything to do with building solutions for a cleaner, more sustainable world. Her expertise was centered around industrial waste and wastewater treatment, and projects Emma was involved with included developing solutions utilizing algae for treatment of nutrients in wastewater, the use of organic materials for handling pollutants and biogas production.
Of work as Product Line Manager in ABB Power Generation working with water treatment, Emma said: “It was work where there’s great opportunity for delivering critical services in a much more environmentally friendly way.”
Emma joined Northvolt in its earliest days as Chief Environmental Officer, motivated by the combination of challenge, opportunity and meaning.
“Everything should be electrified for the simple reason that the most sustainable way to transport energy is through the electricity grid. It depends on local conditions how you produce, wind or solar or biogas for instance, but distribution should be harmonized.”
“Electrification like this provides the quickest route to decarbonizing across multiple sectors of transport, heating, power and so on.”
In line with current mainstream thinking within the green energy industry, Emma recognized that batteries play a pivotal role in this future but extended this with consideration for the environmental aspect of batteries.
“It’s clear to me that batteries are the enabler to so much of that vision for electrification, but there are better and worse ways to build a battery from an environmental perspective. At its heart, Northvolt is about developing the very best possible way to build a battery – a way that does not compromise with other sustainability aspects. That’s what my team and I are working towards.”
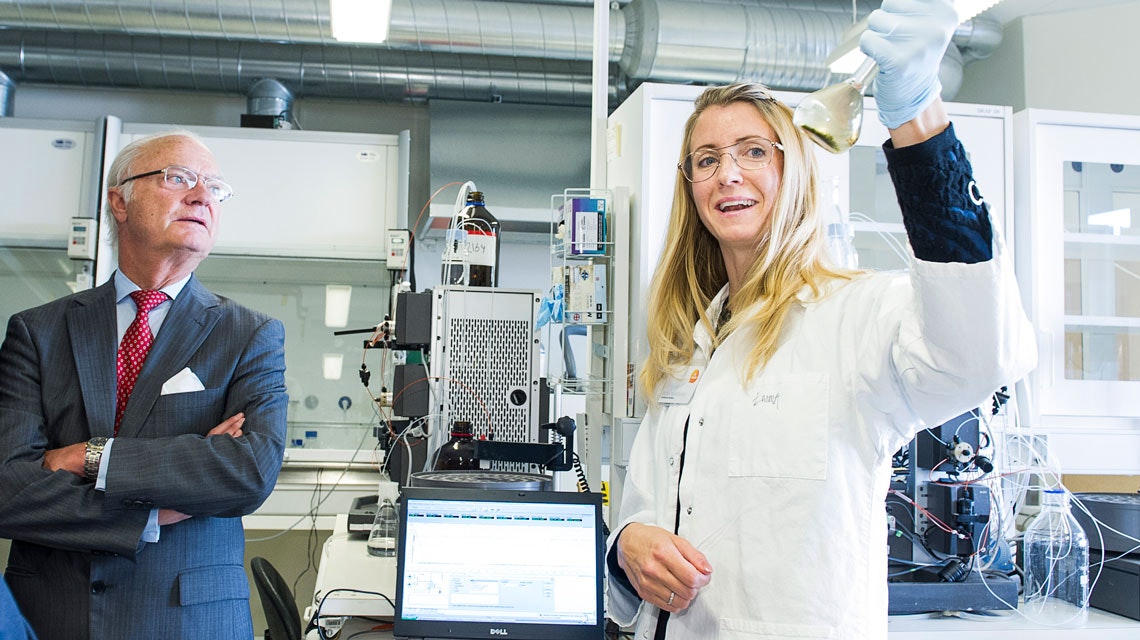
October 2, 2015, His Majesty King Carl XVI Gustaf of Sweden visits MDH and the lab of Emma Nehrenheim. Photo reprinted with permission from photographer, Jonas Bilberg, and MDH.
Joining Northvolt
At its core, Emma’s role carries responsibility for Northvolt’s environmental and sustainability agenda – it’s no small duty.
“What we’re doing with building a green battery has simply never been done before,” she remarks. “That’s challenging of course, but it’s also incredibly motivating. Because we’re working towards something entirely new, there’s scope for fresh solutions and approaches to be applied. Actually, it’s more than scope; I believe it’s a fundamental necessity that we build our away to a green battery.”
With the Northvolt mission to produce a template for how to establish a sustainable model for battery manufacturing, the work of Emma and her team necessarily extends well beyond environmental compliance.
“That’s something Peter Carlsson (Northvolt’s CEO) explained to me early on, that I was to take an engineering and technical perspective in this path. An early goal was to assemble a team of experts who could deliver what we required.”
The solutions
From the outset it was understood that the broad solution to reducing the environmental footprint of Northvolt batteries rested in vertical integration – that is, the incorporation of much of the battery manufacturing supply chain into the operations of Northvolt itself, rather than outsourcing processes to external suppliers.
“What we are trying to accomplish when it comes to a vertical integrated factory is to take everything that comes out of a machine and recirculate it. So that may be heat, which we can use to heat up another machine. If it’s water, let’s recycle it. If it’s a chemical, recycle it. In this way, with vertical integration we have control over the processes that contribute to the environmental footprint of our batteries.”
The idea is to build flows as small as possible, Emma explained, describing how early work involved analyzing every step of the manufacturing process on the hunt for every stream that could be optimized in this way.
“Nothing is too small to work with, and everything has value when it comes to ensuring the most efficient manufacturing footprint possible.” The circular approach extends to the larger scale too. “The largest flow we’re working with is the battery itself. Here we’re developing a well-defined end-of-life strategy for batteries.”
Motivating all of this is hard truth: with the huge growth pitched for lithium-ion battery market (90% of which will go to electric vehicles by 2025), some 11 million tonnes of batteries will be discarded by 2030.
“Looking ahead to where we’re going, it’s clear that we have to establish a new standard not only for how we manufacture batteries, but how we recycle them too. Recycled lithium-ion batteries will be an agent of change in the energy world and a critical piece of the puzzle in our fulfilment of the global sustainable development ambitions.”
On collaboration
A vital aspect driving Northvolt’s approach to innovation, Emma explained, is to recognize the value of partnership: “Northvolt’s vision is incredibly ambitious, and it’s one that requires collaboration. We cannot know everything, but by drawing on the expertise of groups outside the company we can bring unique insights to the table.”
“The key is to set up the right partnerships with the right people, so that together we can work with the values we have in play. That’s really going to make a difference for us.”
“We’ve brought a lot of world-class people in-house, from around the planet, but even still, partners like ABB are key to our work.”
As it happens, Emma’s previous employer, ABB, remains in her world, but now as a key partner to Northvolt, involved with developing automation technologies that are critical to the Northvolt vision.
In Västerås, where Northvolt’s demonstration line and R&D facility, Northvolt Labs, is being established, ABB is building a strong automation cluster and embracing a highly collaborative approach to development.
Commenting on the partnership between the two companies, Emma says: “ABB is very ambitious in its own rights, and there is little doubt in my mind that they see the Northvolt venture as a challenge they were very excited to engage with. We’re in this together, and they represent a major asset to Northvolt.”
Collaboration extends further to include work with academic groups too. “We also look forward to discussing what we can do together in automation and robotics with academia, where MDH has cutting-edge expertise,” says Emma.
In another context, Northvolt has been working with the Industrial Materials Recycling group at Chalmers University of Technology to develop sustainable and industrialized technologies for large-scale batteries recycling processes. Other partnerships geared towards developing next-generation recycling processes include ones with KTH Royal Institute of Technology in Stockholm and Aalto University in Finland. “We have to stay prepared in respect to optimizing processes and keeping up the momentum on our industrialization optimization.”
The bigger picture
For Emma, there is a certain context to the philosophy driving her. “What we’ve learnt from the history of environmental work in general is that usually we are hitting things far too late. We see the problem too late. So carbon footprint and climate change is important to us now, clearly, but we need to consider what will be critical in ten, twenty, thirty years. Here, I think water usage, pollution in terms of chemistry…these are some of things we need to take great care over today.”
“If we are to stay modern after production is up and running, we need to keep track of our compromises.”
Asked if she sees adoption of similar sustainable approaches in the battery manufacturing industry at large, Emma offers a definitive answer: “No I don’t see that at all. In fact, it is quite the other way around. We see plants being established, even here in Europe, where they will be leaching into the environment in a way that we would never do.”
It’s a worrying circumstance considering the number of battery factories under development. All the more reason, according to Emma, that Northvolt succeed. “If we can prove this model for manufacture is viable, there should be no question left for anyone taking decisions over how to deploy new manufacturing capacity.”
At this point in such a conversation, there is natural tendency to veer towards the financial implications of a sustainable solution. “I have two points I like to highlight on that matter,” says Emma. “
Firstly, what we have found is that with these kinds of investments, they create byproducts that have great value. So the down payment period is actually far shorter than you would think. It’s not bad economy at all, provided you find the right investments.”
“Second, sustainable assurances of the sort Northvolt will be providing, are almost certainly going to be a hygiene factor for car manufacturers and other OEMs. So there will be a premium and demand for this.”
Encouragingly, as Emma explained, recognition of these points is already apparent across the industry, and in customer segments. “Customers are already communicating this to us. And this has changed. If I go back two years, I have a feeling they were more interested in typical battery metrics; in function, safety, price and so on. Now I hear that if a battery provider is even roughly on par with cost and quality, but have a better sustainable footprint, they win every time.”